防腐蚀涂层缺陷之气泡(转)
防腐蚀涂层耐蚀的主要因素就是涂层具有优异的惰性、完整性和致密性。如果涂层被破坏或者致密性不好,就会引起外部介质(如水、水汽及腐蚀性物质等)渗透浸入,直接与基层发生电化学或者其他反应,产生腐蚀现象,导致防腐蚀失效。其中涂层气泡是造成涂层完整性及致密性破坏的“元凶”,除了影响涂膜的外观效果;还会形成其他涂层缺陷,如缩孔、针眼、疵点、鱼眼等弊病。因此,预防涂层气泡的产生及其处理方法,是防腐蚀涂层实现长久使用效果的重要保障。
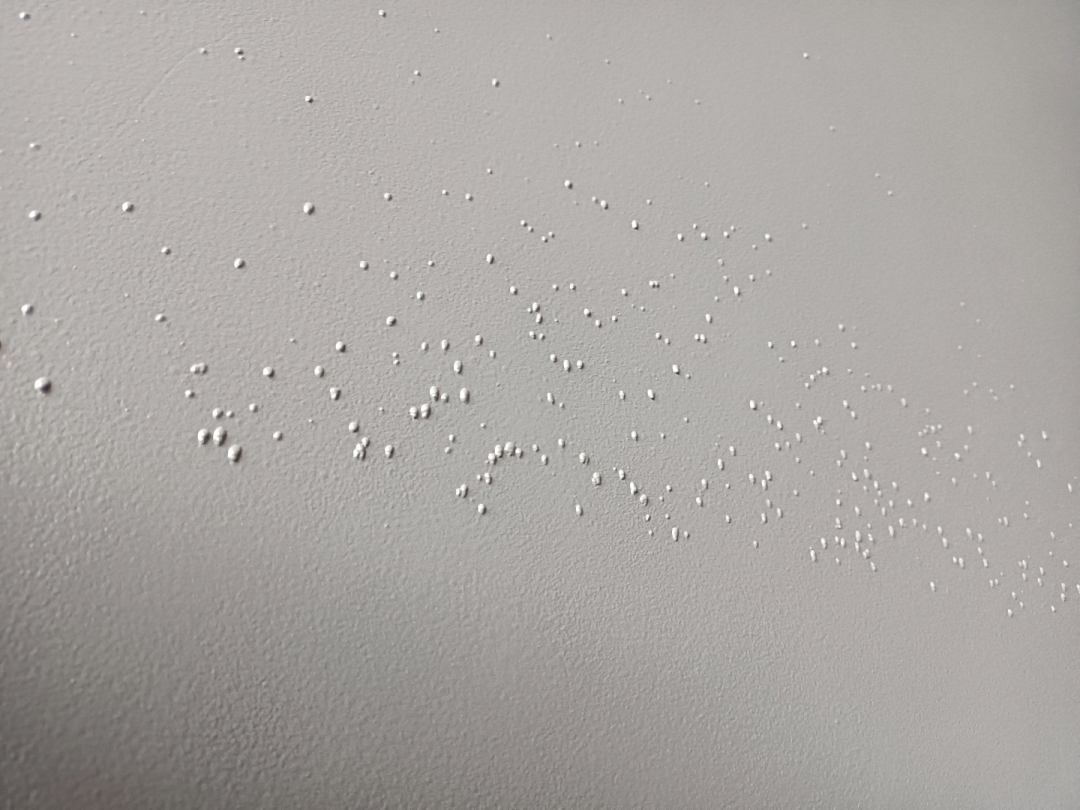
防腐蚀涂层气泡是细小的可见的数毫米直径的空心体,并在外力的作用下进入涂料液体中,被液体相互隔离成一个非均相体系。涂料中的气泡是气体在涂料液体中的一种分散形式,是一种典型的热力学不稳定两相体系。因为气泡的存在增加了涂层体系的表面积,增加了体系的能量,当气泡破裂后,体系中的总表面积大大减少,相应的能量也随之降低,因此存在气泡的涂料始终处于热力学不稳定的状态中,对防腐蚀涂层的防腐性能,耐候性能及附着力,美观性等破坏性很大。
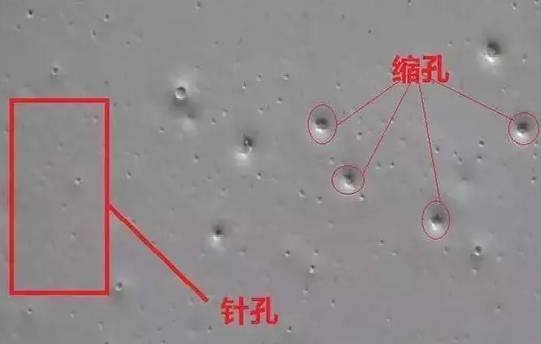
涂层气泡大小不一样,气泡内部含有各种各样的物质,可以含有液体、蒸汽、其他其他或者是结晶物。气泡的大小依赖于防腐蚀涂料与基层表面附着力、泡内介质的压力及为了和涂料基层附着力保持相对平衡而将涂膜拉伸反向顶起的程度。气泡有泡和泡沫两种形式,一般情况下溶剂型防腐蚀涂料容易产生泡;而水性防腐蚀涂料更容易产生泡沫。防腐蚀涂层气泡可以分成膨胀气泡和腐蚀气泡两种形式,通常溶剂型防腐蚀涂料涂布成膜后,残留的溶剂含在涂料中,这些微量的溶剂可以存在很长时间,当温度变化时,涂层局部失去附着力,受泡内气体或者液体压力就会离开基层,进而鼓起涂膜,形成圆形凸起。这种变形可以在涂膜干燥过程中消失也可以永久性存在。所以防腐蚀涂层气泡产生条件离不开涂层具备的透水透气性;离不开涂层与基层存在着缺陷或者是隔离层(如润湿不好、漏涂、灰尘、油污、水及其他可溶性杂质)。当温度升高时气泡会膨胀扩大,到达极限时就会破裂;另外频繁的温差起伏变化,也会造成涂膜疲劳开裂。
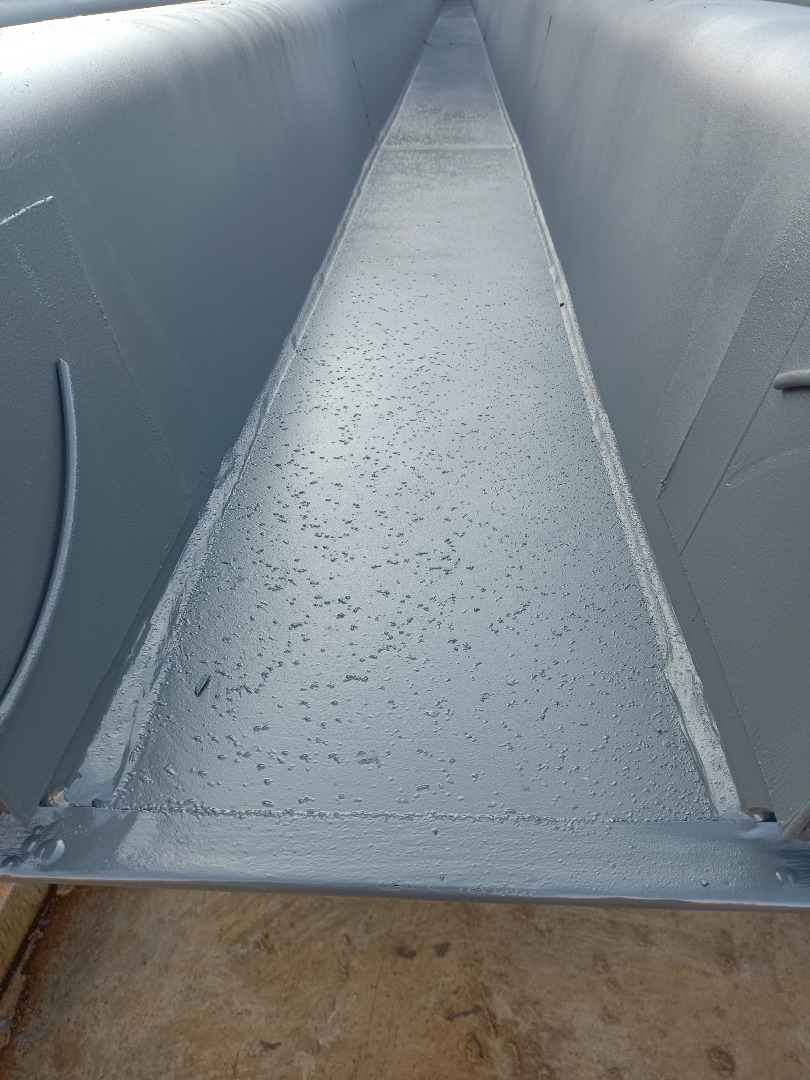
防腐蚀涂层气泡的形成原因非常复杂,有涂料自身的原因,也有工程施工的原因,还有环境、基层等多方面的因素。根据长期的涂料生产及施工实践经验,防腐蚀技术人员总结了以下一些重要的原因:
1.基层表面处理不好。基层存在锈蚀层,氧化皮,污染物质,可溶性盐,灰尘,水分,油污等,可以说是涂层与基层的隔离层,温度升高形成膨胀,产生气泡。
2.涂层中残留的溶剂。溶剂型防腐蚀涂料涂装形成的湿膜,还有10%的挥发性溶剂,大约90%的溶剂已经挥发到大气中。如果溶剂挥发不好会残留溶剂,随着温度升高,溶剂会产生蒸气压,形成气泡。
3.薄层涂膜容易渗透外部介质。当涂装后的涂层达不到规定的厚度,而且很薄,而且处于潮湿环境下时,将会发生介质渗透现象,特别是在湿热环境下形成的蒸气压和渗透压同时作用加剧了气泡的产生。
4.雨天或高湿度环境下施工。雨天或高湿度环境下涂装,基层表面就会集聚水汽或者水珠,这些留存在涂层内的水汽水珠遇有温度变化时就会汽化,顶起涂层形成气泡。
5.多孔性基层残留的空气。一些多孔性基层,如水泥、木材等孔隙中有空气存在,涂层因溶剂挥发被顶起,形成气泡,而且温度较高时容易出现,生成的速度非常快,容易破裂而露出基层。
6.涂料中含有可溶性物质。防腐蚀涂料中含有可溶性颜填料,通过渗透作用吸收透过涂层的水分,潮气及其他液体,变成溶液,温度变化膨胀后形成气泡。
7.防腐蚀涂层及阴极保护氢气的产生。气泡还发生在阴极保护区域的涂料层,这是因为在阴极保护区域的涂层下金属基层表面会有氢气产生,当产生的氢气量达到一定的体积后,就有足够的压力顶起涂膜,形成气泡。
8.底面漆不配套。预涂防腐蚀底漆后,使用不配套或者高性能的防腐蚀面漆罩面时,也会出现气泡现象。主要原因就是底漆附着力不好,高性能面漆中的溶剂就会“咬底”引起底漆脱离基层,产生气泡。
9.腐蚀介质与基层材料反应。一些有机酸,无机酸,碱渗透到防腐蚀涂层(涂层太薄)并与钢材、苛性碱与锌和铝等发生反应产生氢气,形成气泡。
10.防腐蚀涂层外干内湿。防腐蚀涂层底漆未干就涂装下一道涂料(如中间漆或者面漆),继续挥发的溶剂膨胀后产生气泡。
11.防腐蚀涂料表面挥发太快。一些防腐蚀涂料使用了挥发性强的溶剂,表面涂层挥发过快而底漆溶剂挥发不畅,形成气泡。
12.防腐蚀涂料粘度太高。涂料粘度太高,润湿性能不好,附着力不够,空腔膨胀形成气泡。
13.基层温度过高。防腐蚀施工中,基层温度过高时,防腐蚀涂料中的溶剂挥发迅速,顶起涂层形成气泡。
14.金属底漆未做封闭。防腐蚀施工中,金属底漆使用比较多的就是富锌底漆,其成膜后的涂层比较粗糙,而且存在孔隙。这些孔隙必须进行填充封闭,如果在没有封闭的涂层上面继续涂覆中间漆或者面漆,一定会产生气泡。
15.反应型防腐蚀涂料释放出副产物。一些固化反应型防腐蚀涂料如采用异氰酸酯固化剂型聚氨酯面漆或者氟碳漆,固化反应需要释放二氧化碳,如果涂层表干非常快或者单道涂层过厚(>45μm/道),很容易形成聚集性致密的气泡。
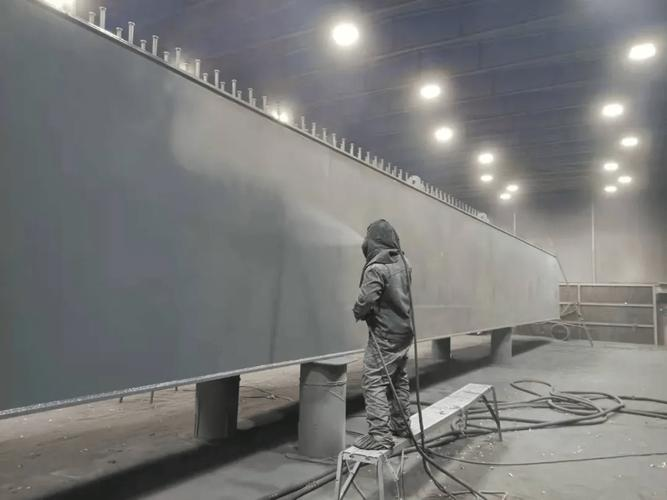
防腐蚀涂层气泡的原因虽然比较复杂;但是离不开两个原因,就是涂料自身的原因(如生产过程控制不严,原材料质量有瑕疵等)和涂料施工的原因(如管理松散,不按照设计或者规范操作)。预防和控制防腐蚀涂料气泡的产生,必须保证涂料产品的质量和加强涂装施工管理,严格按照标准规范和设计要求控制好涂每一道涂层。按照上述防腐蚀涂层气泡产生的原因,可以对标采取有效的解决方案,避免气泡的产生,保证防腐蚀涂层的完整性、致密性和美观性。具体方法如下:
1.彻底,干净的处理好防腐蚀基层表面,利于防腐蚀涂料的良好附着。
2.选择合适的涂料稀释剂、溶剂,保持正常的挥发性,并使涂层完全干燥具有很好的硬度,无任何溶剂残留。
3.按照设计和规范规定要求,保证防腐蚀涂层具有一定的厚度,抵抗蒸气压和渗透压引起的气泡。
4.防腐蚀涂层施工时,选择晴朗的天气进行,阴雨天及湿度>85%时暂停涂装操作,避免水汽进入涂层。
5.涂装多孔材料时,应先涂刷渗透性好的封闭底漆,驱除孔隙内的残留空气、溶剂等残留物。
6.防腐蚀涂料生产时,合理选择颜填料,避免添加可溶性物质。
7.防腐蚀工艺采用阴极保护和涂层复合方案时,底漆选择友好型耐阴极剥离涂料,避免气泡的发生。
8.防腐蚀涂层施工时,底漆、中间漆及面漆必须相互配套,不得使用不相容或者相互反应的涂料覆涂。
9.涂层未完全干燥或者涂膜厚度不足,严禁一些化学物质如酸、碱、盐等与涂层表面接触,必须进行后续养护,避免因为化学品的浸入产生气泡。
10.防腐蚀涂层施工时,必须保证每一道涂层完全干燥,只有前道涂层固化干燥后才能覆涂后道涂层。
11.防腐蚀涂料配方及生产,应该考虑和选择最佳的溶剂,合适的稀释剂,不得使用强挥发性溶剂和稀释剂。
12.防腐蚀涂料粘度太高,可以使用合适的稀释剂进行“开稀”,将粘度调整到具有可操作性及一定润湿效果的程度,提高涂层的整体附着力。
13.当基层温度过高时,尽量避免涂装施工,或者使用带温涂装的特种高温漆,避免因油漆溶剂挥发太快顶破涂膜形成气泡。
14.富锌底漆或者金属热喷涂涂层,因为存在空隙,并且留存空气,必须使用渗透性底漆进行封闭,排尽内腔的空气,才能进行后续涂层的施工。
15.防腐蚀涂层使用反应固化型油漆时,可以选择涂层表干不要太快的产品,涂装厚度也不要太厚,建议单道厚度在45μm以下,以释放反应过程中产生的气泡。
通过防腐蚀涂层气泡缺陷产生原因分析及预防措施,可以基本抑制涂层气泡的产生。如果一旦涂层不可避免的产生了气泡,可以进行有效的处理,工艺方法是用水砂纸将涂层气泡打磨,保持气泡边缘与周边平整度一致,并清理干净。清理后的表面再用稀释剂或者溶剂擦洗一遍,将同种底漆与重晶石粉(200目)调成腻子,批刮一遍,干燥后,打磨平整,清理干净后再整体涂刷一道面漆。虽然处理后的防腐层能够满足耐蚀及美观要求;但是在实际防腐层涂装施工中必须将预防气泡的产生放在第一位,无论从施工成本还是质量效果都是预防重于处理,决不能本末倒置。
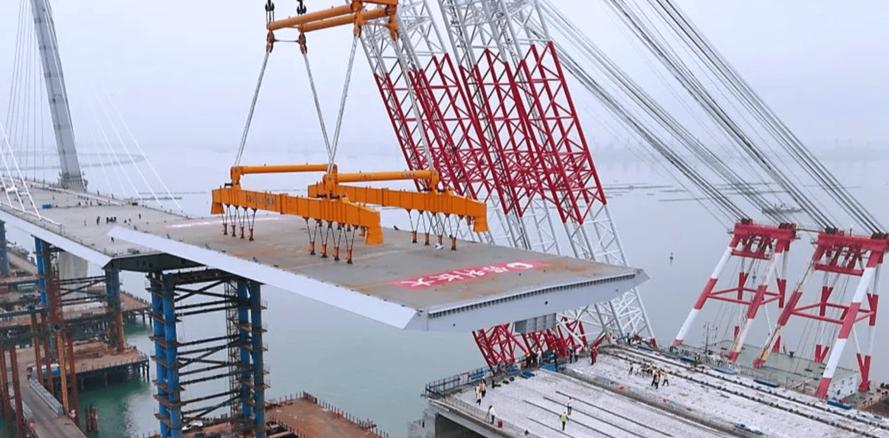
防腐蚀涂层失效的原因很多,很复杂,有的失败案例也让防腐蚀施工技术工程师百思不得其解;但其中常见的缩孔、针眼、疵点、鱼眼、橘皮等涂层缺陷却是气泡“惹的祸”。这些缺陷也是破坏防腐蚀涂层完整性、致密性及装饰性的主要原因,避免的方法就是预防涂层气泡的产生。防腐蚀施工技术人员弄清楚气泡产生原因,采取积极有效的措施控制气泡的发生,就可以大大的提高防腐蚀涂层耐蚀水平,满足长效防腐的应用要求。